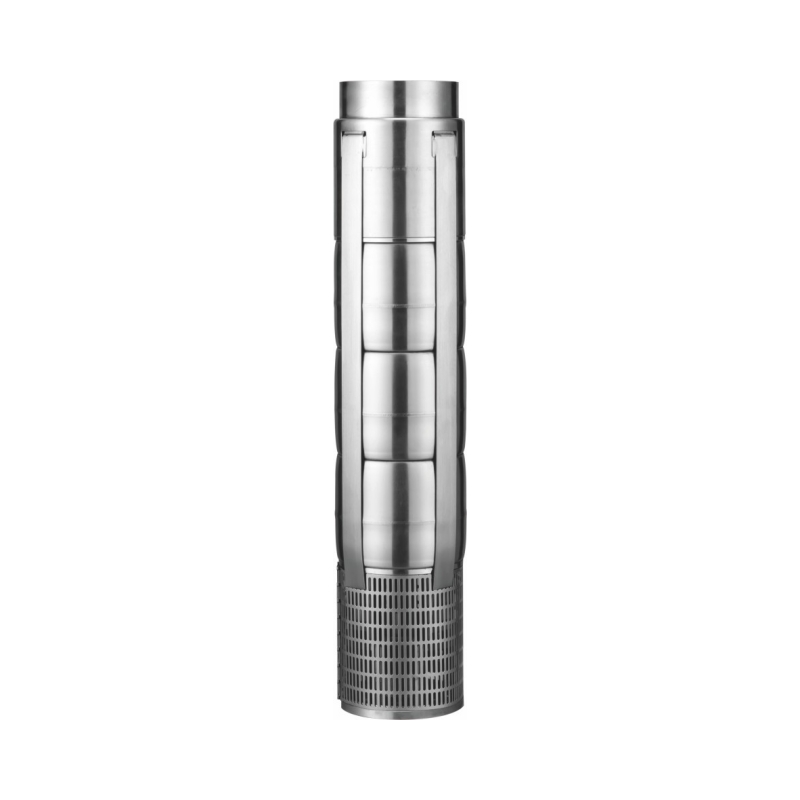
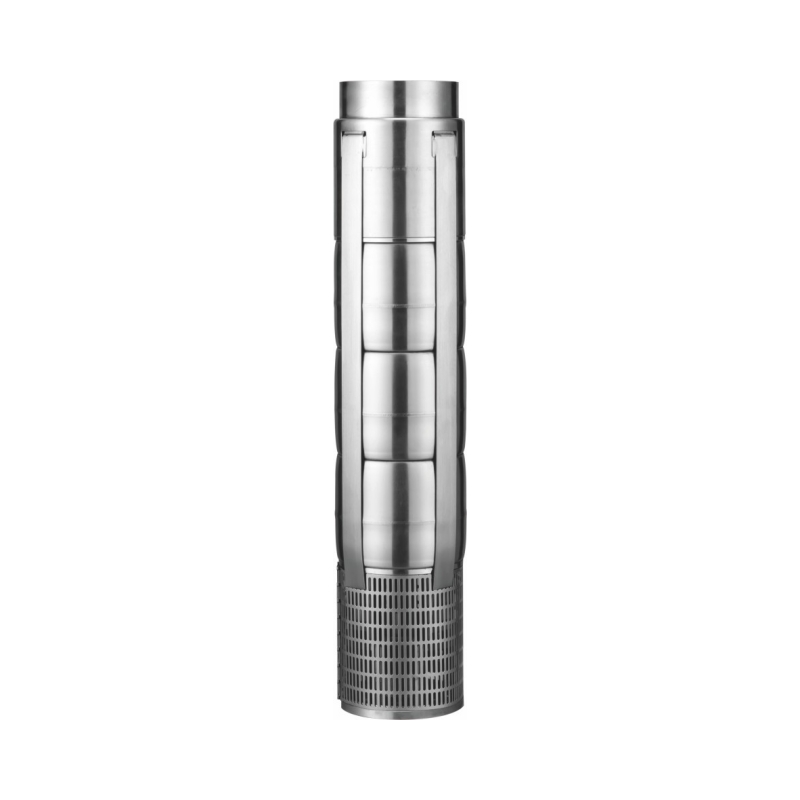
Cast stainless steel water pumps are widely used in various fields (such as chemical engineering, marine, food processing, etc.) due to their material and process characteristics. Their advantages mainly stem from the performance of stainless steel materials and the advantages of casting processes. The following is a detailed analysis of the advantages:
Excellent corrosion resistance
Material properties: Stainless steel (such as 304, 316, CF8M, etc.) contains alloy elements like chromium, nickel, and molybdenum, which form a passive film, enabling it to resist corrosion from water, acids, alkalis, salts, and other media.
Advantages of casting process: Casting in one piece reduces welds and joints, avoiding failure caused by intergranular corrosion at the welding sites, making it particularly suitable for corrosive liquids (such as seawater and chemical fluids).
2. High strength and durability
Structural stability: The casting process forms the pump body as a whole through molds, making the internal structure of the pump body dense, reducing defects such as pores and cracks, and enhancing mechanical strength and pressure resistance.
Wear resistance: Stainless steel has a relatively high hardness. After casting, it can be further heat-treated to enhance the pump body's wear resistance against granular media (such as water containing sand and silt), thereby extending its service life.
3. Adaptation to Complex Working Conditions
Wide Temperature Range: Stainless steel has excellent high-temperature resistance (typically capable of withstanding temperatures from -20°C to 400°C), and the cast structure is less prone to deformation at high temperatures, making it suitable for the transportation of hot water, steam, or low-temperature fluids.
Suitable for high-pressure environments: The casting pump body has uniform wall thickness, can withstand higher pressure, and reduces the risk of leakage.
4. Design Flexibility and Performance Optimization
Complex Flow Path Forming: The casting process can precisely manufacture complex geometries such as impellers and volutes, optimize hydraulic design, and enhance pump efficiency (such as reducing cavitation and turbulence).
Customized production: The molds can be flexibly adjusted to meet the requirements of different flow rates and head heights, and are suitable for special industrial scenarios.
5. Low Maintenance and Long Service Life
Anti-pollution and Easy to Clean: The stainless steel surface is smooth, not prone to scaling or bacterial growth, and easy to clean, meeting the hygiene standards of the food and pharmaceutical industries.
Reduce downtime costs: Corrosion and wear resistance reduce the frequency of component replacement, resulting in lower overall costs over the long term.
6. Environmental Protection and Economy
Recyclability: Stainless steel materials can be 100% recycled, in line with the trend of green manufacturing.
Low life cycle cost: The initial investment may be higher than that of cast iron pumps, but in the long term, due to its longer service life and less maintenance, the total cost is more advantageous.
Typical application scenarios
Chemical industry: Conveying corrosive media such as acids, alkalis, and organic solvents.
Marine engineering: seawater cooling, ship ballast water pumps.
Food and pharmaceuticals: Hygienic fluid transfer to prevent contamination.
High-temperature systems: boiler feed water, hot oil circulation.
Summary
Casting stainless steel water pumps, through the combination of materials and processes, stand out in terms of corrosion resistance, structural strength, adaptability and service life, and are particularly suitable for reliable operation under harsh working conditions. When users make a choice, they need to comprehensively consider the characteristics of the medium, working pressure, temperature and cost to achieve the best performance match.
Model No. | Motor | Q(m³/h) | Flow(n≈2850r/min) | Pump Length(mm) | Pump Weight(kg) | Outlet Diameter | ||||||||
kW | HP | 60 | 80 | 100 | 120 | 140 | 160 | 180 | 200 | |||||
QP120-1 | 9.2 | 12.5 | H(m) | 20 | 19 | 18 | 17 | 16 | 14 | 12 | 9 | 530 | 25.4 | DN150 6" |
QP120-2 | 18.5 | 25 | 40 | 38 | 36 | 34 | 32 | 28 | 24 | 18 | 690 | 34 | ||
QP120-3 | 30 | 40 | 60 | 57 | 54 | 51 | 48 | 42 | 36 | 27 | 850 | 42.5 | ||
QP120-4 | 37 | 50 | 80 | 76 | 72 | 68 | 64 | 56 | 48 | 36 | 1010 | 51 | ||
QP120-5 | 45 | 60 | 100 | 95 | 90 | 85 | 80 | 70 | 60 | 45 | 1170 | 59 | ||
QP120-6 | 55 | 75 | 120 | 114 | 108 | 102 | 96 | 84 | 72 | 54 | 1330 | 71.5 | ||
QP120-7 | 63 | 85 | 140 | 133 | 126 | 119 | 112 | 98 | 84 | 63 | 1490 | 80 | ||
QP120-8 | 75 | 100 | 160 | 152 | 144 | 136 | 128 | 112 | 96 | 72 | 1650 | 88 | ||
QP120-9 | 90 | 125 | 180 | 171 | 162 | 153 | 144 | 126 | 108 | 81 | 1810 | 96.5 | ||
QP120-10 | 90 | 125 | 200 | 190 | 180 | 170 | 160 | 140 | 120 | 90 | 1970 | 105 | ||
QP120-11 | 110 | 150 | 220 | 209 | 198 | 187 | 176 | 154 | 132 | 99 | 2130 | 113 | ||
Model No. | Motor | Q(m³/h) | Flow(n≈2850r/min) | Pump Length(mm) | Pump Weight(kg) | Outlet Diameter | ||||||||
kW | HP | 90 | 110 | 130 | 140 | 150 | 170 | 190 | 210 | |||||
QP150-1 | 13 | 18 | H(m) | 25 | 24 | 23 | 21 | 20 | 18 | 17 | 14 | 530 | 25.6 | DN150 6" |
QP150-2 | 25 | 34 | 50 | 48 | 46 | 42 | 40 | 36 | 34 | 28 | 690 | 34.5 | ||
QP150-3 | 37 | 50 | 75 | 72 | 69 | 63 | 60 | 54 | 51 | 42 | 850 | 43 | ||
QP150-4 | 55 | 75 | 100 | 96 | 92 | 84 | 80 | 72 | 68 | 56 | 1010 | 51.5 | ||
QP150-5 | 63 | 85 | 125 | 120 | 115 | 105 | 100 | 90 | 85 | 70 | 1170 | 64 | ||
QP150-6 | 75 | 100 | 150 | 144 | 138 | 126 | 120 | 108 | 102 | 84 | 1330 | 72.5 | ||
QP150-7 | 90 | 125 | 175 | 168 | 161 | 147 | 140 | 126 | 119 | 98 | 1490 | 81 | ||
QP150-8 | 110 | 150 | 200 | 192 | 184 | 168 | 160 | 144 | 136 | 112 | 1650 | 90 | ||
QP150-9 | 110 | 150 | 225 | 216 | 207 | 189 | 180 | 162 | 153 | 126 | 1810 | 98 |